Global Supply Chain & Inventory Pro: Master Certification
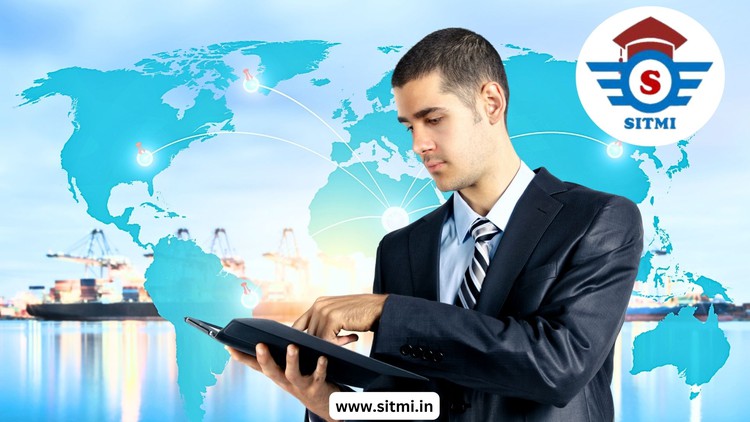
Why take this course?
- Supply Chain Analysis - Meaning, Logics & Uses:
Supply chain analysis is a systematic approach to understand the dynamics of supply and demand for products or services. It involves the study of various factors that influence the supply chain network, from procurement of raw materials to delivering the finished goods to the end consumer. The purpose is to optimize processes, minimize costs, and improve customer satisfaction by ensuring timely and reliable product availability.
- VED (Value Engineering Design) Analysis - Meaning, Logics & Uses:
VED analysis is a methodical process used in project management to examine the function of all items in a deliverable from the standpoint of ultimate user needs and to apply the creatively developed alternatives in conjunction with design and/or process to achieve optimum balance between fundamental measures of performance, affordability, and constructability without compromising essential functions or performance.
- SDE (Systematic Design Engineering) Analysis - Meaning, Logics & Uses:
SDE analysis is a structured approach that provides for the systematic design and integration of all elements of an engineering project. It ensures that from conception to delivery, the product or service meets customer requirements in terms of quality, functionality, and cost-efficiency.
- S-OS (Service-Oriented Strategy) Analysis - Meaning, Logics & Uses:
S-OS analysis focuses on adopting a service-oriented strategy within an organization. It emphasizes creating value for customers by integrating products and services into comprehensive solutions that address specific customer needs. This approach aligns organizational processes, resources, and technologies to deliver customized experiences to the end user.
- GOLF (Goal Orientation, Leadership, Functionality) Analysis - Meaning, Logics & Uses:
GOLF analysis is a strategic framework that guides organizations in achieving their objectives by focusing on clear goals, effective leadership, and functional processes. It ensures that every aspect of the business is aligned towards delivering on the defined goals and providing value to stakeholders.
- PQR Analysis - Meaning, Logics & Uses:
PQR analysis stands for Performance, Quality, and Reliability. It is a comprehensive evaluation that assesses an organization's ability to meet performance benchmarks, maintain high-quality standards, and ensure the reliability of its products or services. This analysis helps organizations to continuously improve and align with customer expectations and industry best practices.
Excel Calculation & Automated calculation sheet for ABC, XYZ, HML, FSN, PQR, ABC-XYZ analysis:
Excel can be used to automate various calculations related to inventory management, financial analysis, and performance metrics. By creating formulas and templates, you can streamline the calculation process for key indicators like Safety Stock, Reorder Point (ROP), Economic Order Quantity (EOQ), Min-Max levels, Average Inventory, Cost of Goods Sold (COGS), Inventory turnover ratio (ITR), Days on Hand (DOH), Gross Margin return on investment (GMROII), and more.
Replenishment planning methods & Calculations in Excel:
-
Safety Stock Calculation: Safety stock is the excess amount of inventory held at a warehouse or storage facility to prevent stockouts despite variability in demand. The formula typically involves estimating demand variability and lead time, then applying an appropriate safety stock calculation method such as the EOQ model.
-
Reorder Point (ROP) Calculation: ROP is the inventory level at which a company needs to order more stock. This is calculated based on historical sales data, lead times, and expected demand.
-
Economic Order Quantity (EOQ) Calculation: EOQ is the optimal order quantity that minimizes total ordering and carrying costs. The formula considers fixed costs such as ordering and setup costs, and variable costs related to inventory storage.
-
Min-Max Levels Calculation: This method sets predetermined maximum and minimum inventory levels. The Min-Max and Max-Min-Max system is a two-number system used for inventory control. Case Study of Walmart:
Walmart, the world's largest retailer, has pioneered several supply chain innovations:
- Vendor Managed Inventory (VMI): Walmart uses VMI to maintain optimal stock levels at its stores by providing real-time data to suppliers who then manage their inventory based on sales forecasts.
- CPFR (Collaborative Planning, forecasting and replenishment): This is a collaborative planning tool used by retailers and suppliers like Walmart to optimize the supply chain. It allows for sharing information in a timely manner to ensure better alignment between the supply chain partners.
- IT Technologies Used by Walmart: Technologies such as Radio Frequency Identification (RFID) are used for inventory tracking, and Electronic Data Interchange (EDI) is used for automated data exchange between suppliers and retailers.
- Benefits Achieved by Walmart: The implementation of these strategies has led to significant benefits such as increased efficiency in the supply chain, reduced costs, improved inventory management, enhanced customer satisfaction, and a stronger competitive advantage in the market.
Course Gallery
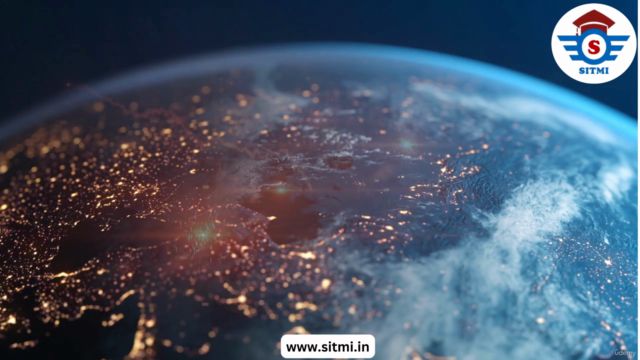
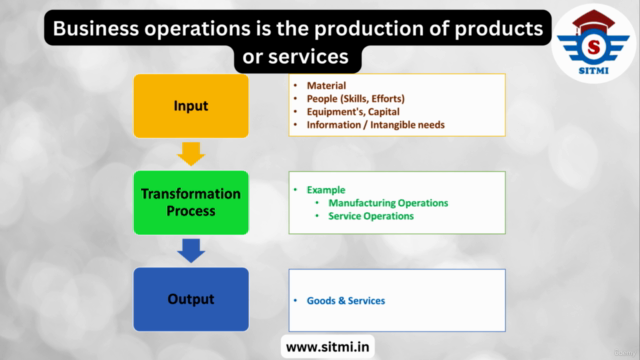
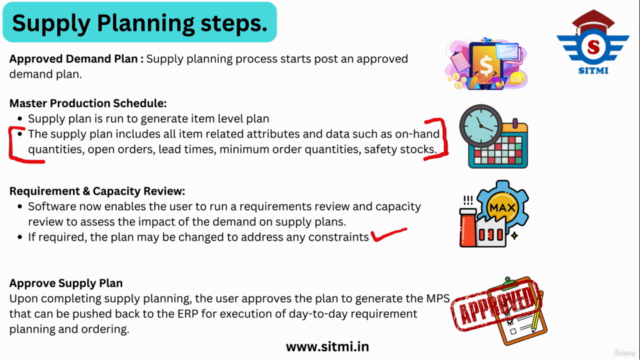
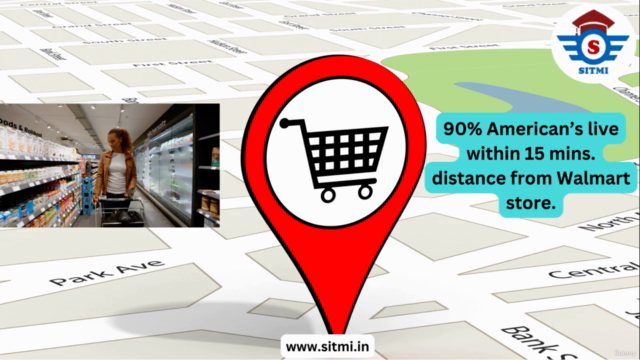
Loading charts...